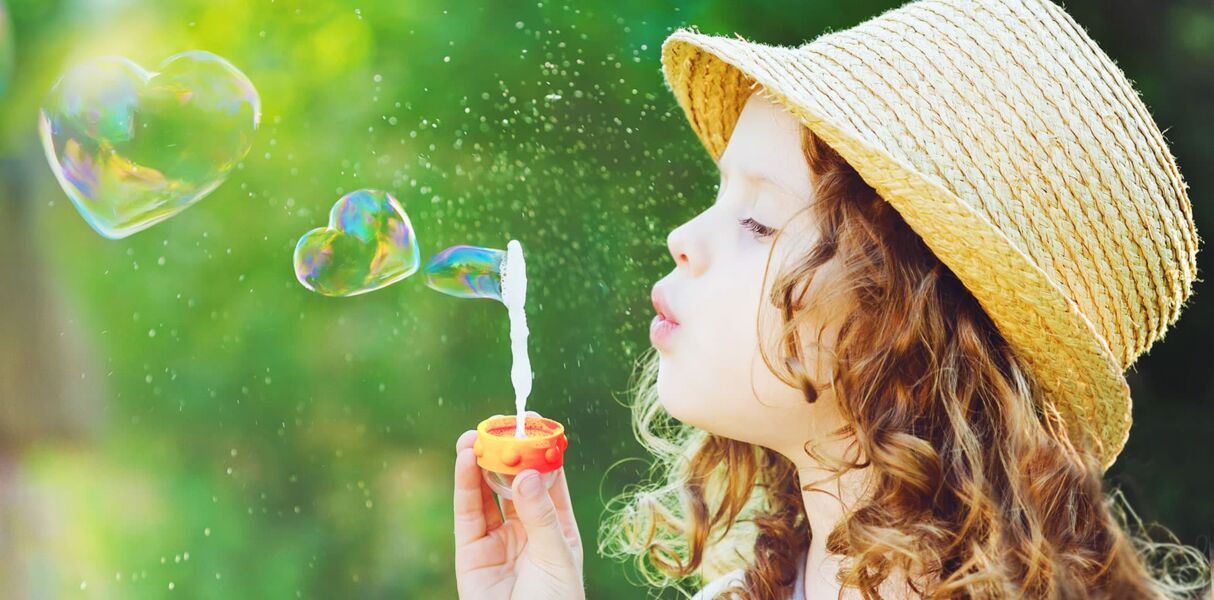
Our responsibility
Valensina GmbH is in the top 5% of companies worldwide according to EcoVadis.
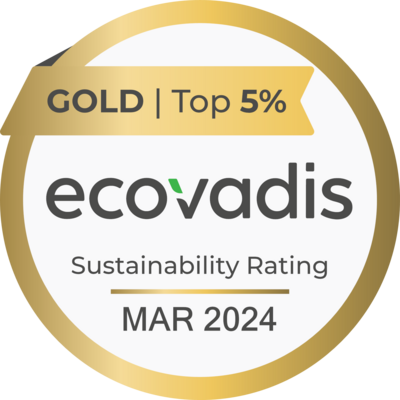
As part of our commitment to society, our people and the environment, Valensina GmbH completes a thorough assessment of its business sustainability practices every year through EcoVadis, a global leader in business sustainability assessments.
The EcoVadis assessment includes 21 sustainability criteria across four core themes: Environment, Labor & Human Rights, Ethics and Sustainable Procurement.
In our latest rating, which was completed on 26.03.2024, we earned a Gold Medal and scored 73 Points, which places Valensina GmbH in the top 5% globally.
Valensina Group 2021–2022 Sustainability Report
We are pleased to present our second sustainability report, which complies with the demanding new requirements of the 2021 GRI Standards. The report gives a detailed picture of progress and developments since our first sustainability report two years ago. We have identified specific sustainability priorities through constructive dialogue with our stakeholders, and remain committed to transparent communication. The new report once again focuses on our packaging, supply chains, environmental policies, use of resources and treatment of our staff. Download the report to learn more!
Visit our trees on Treedom!
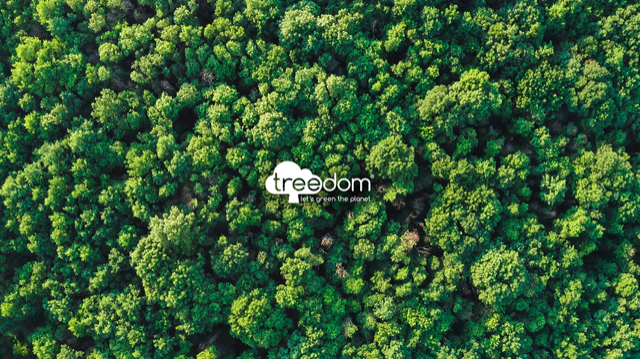
We are planting biodiverse forests in Colombia, Kenya and Guatemala – because we love the idea of doing our little bit to make the planet greener. Our partner Treedom directly finances small-scale agroforestry projects around the world. Treedom’s mission is to create sustainable ecosystems and provide thousands of smallholder farmers with seed funding so they can plant new trees. The fruit from the trees benefits the farmers, their families and their local communities by creating sustainable jobs, fair income opportunities and long-term food security. Treedom is the only platform in the world that allows users to remotely plant trees and follow their progress online. To increase participation, transparency and visibility, every tree is photographed and geolocated after planting and given its own profile page which tells that tree’s own unique story.
Want to learn more about the trees we’ve planted through Treedom? Then click here.
Together for a sustainable fruit juice sector
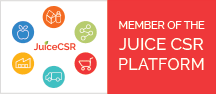
Juice CSR (Corporate Social Responsibility) Platform
Since 2015, we have been a member of the Juice CSR Platform, a sustainability initiative co-initiated by the European Fruit Juice Association (AIJN), which was created specifically for the fruit juice industry. The aim of this initiative is to inspire and support all participating companies and organisations in the industry to integrate their social responsibility into their business activities and their core strategy.
Thanks to global networking within the sector, we can master the challenges together. More specifically:
– Promoting a common understanding of CSR
– Overcoming social, ecological and economic problems together
– Giving priority to CSR and sustainability aspects
Like our suppliers, we strictly adhere to the Code of Business Conduct issued by the AIJN, which ensures that the internationally applicable minimum standards for human rights, work and the environment are not only observed, but also promoted and further improved throughout the value chain. In May 2024, we also published our own Supplier Code of Conduct.
Supplier Code of Conduct Sustainability
As one of the leading family-owned companies in the fruit juice industry, we are aware of our corporate responsibility along global supply and value chains and actively assume this responsibility. With passion, motivation and joy, we pursue the goal of meeting the highest standards in everything we do. Our business activities, as well as those of our suppliers and business partners, must be in harmony with human rights and environmental protection in order to continuously promote sustainable business practices. We focus on long-term business relationships based on partnership and specify our expectations in this Supplier Code of Conduct Sustainability.
Making our packaging more sustainable
Since February 2019, we have been using PET bottles with between 30 and 100 per cent post-consumer recycled content (rPET). rPET is a secondary raw material made from used PET bottles, which are cleaned and granulated. This closed-loop recycling is based on the “bottle-to-bottle” principle. rPET has almost identical chemical properties to PET and can be recycled multiple times. However, rPET is currently relatively expensive due to the recycling process. The available supply is also limited. In recent years, between 42 and 54 per cent of our PET bottles have been made with rPET. Our goal is to increase that proportion, though whether we can do so will depend on how the market situation develops: the supply of rPET is expected to become even more limited in 2025 when statutory minimum requirements come into force.
We are also continuously working to reduce the weight of our packaging. Between 2019 and 2022, we managed to cut the weight of our one-litre PET bottles by 10.7 per cent.
We engage in regular dialogue with our customers and suppliers about how we can make our packaging materials more sustainable – without compromising on the highest standards of product and transport safety.
Helping out our six-legged friends
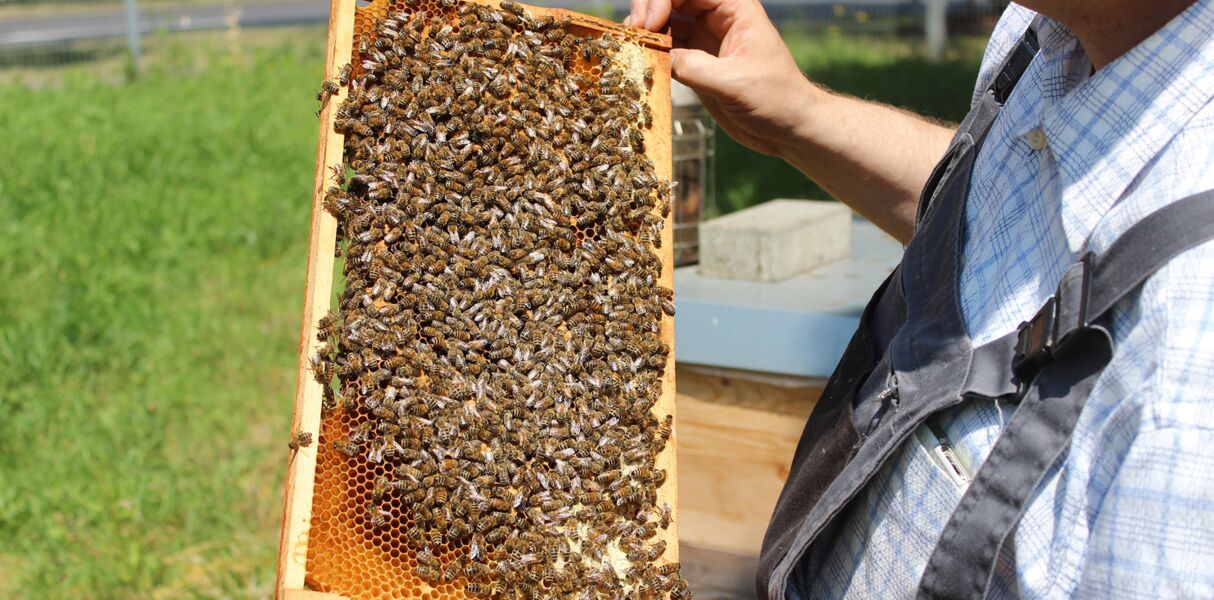
Wild bees and other pollinators are essential for practically every ecosystem on earth. But their habitats are rapidly declining – so action is needed. That’s why in 2014 Valensina became an official partner of Deutschland summt!, an initiative that aims to raise awareness of the vital importance of bees.
We’ve turned the grounds of our headquarters in Mönchengladbach into an apian paradise, with bee-friendly plants, apple trees and a wild bee hotel. Our hives – surrounded by a magnificent garden of wildflowers and herbs – are now home to ten honeybee colonies. Learn more here.
Our own biogas plant
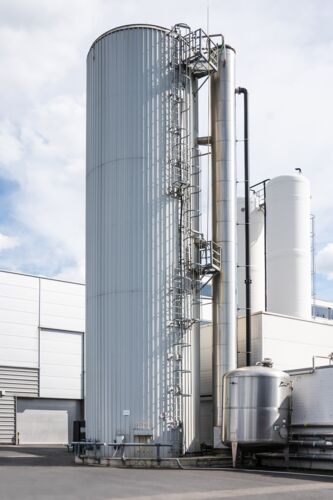
At our Mönchengladbach location, we operate a biogas plant together with the company Remondis. Using active microorganisms, we metabolise the biomass from our wastewater and turn it into biogas.
We use the biogas in one of our steam boilers. We produce hot water with the steam and use it e.g. to sterilise the filling plants, pasteurisers etc.
We produce approx. 174,000 m3 biogas a year, which is enough to run our heating system all year round.
Our wells in Vechta
At the our Vechta site, the water supply is ensured by 3 deep wells (43 meters deep) – we are entitled to extract 800,000 m³ per year.
To monitor the level of the valuable groundwater, our employees regularly check the current status at 12 pilot wells around the premises. In collaboration with an external geo-laboratory, an end-of-year report is then compiled from the various parameters.
The well water is first treated in a sophisticated filtration process using gravel filters. We then let it pass through 3 reverse osmosis systems before using the high-quality water for our products. The water used to cool our production processes is reused sustainably in internal cleaning processes. Our water is subject to strict monitoring by our laboratory.
Our wastewater disposal
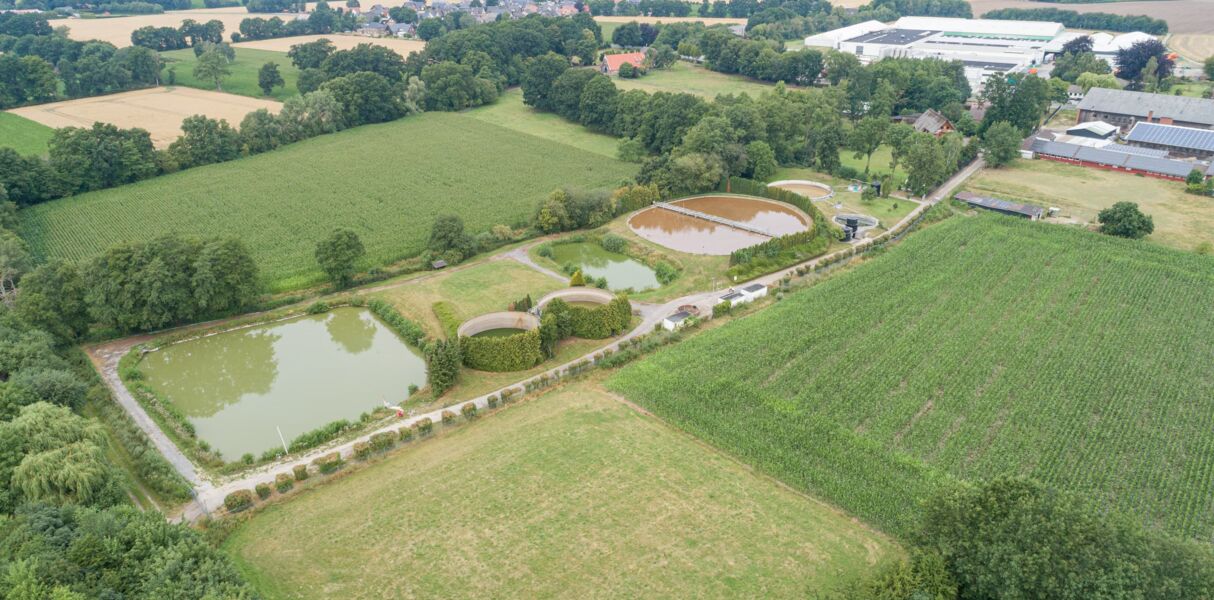
Our plant in Vechta has its own sewage treatment plant for cleaning the production wastewater. The plant has a capacity of 15,000 residential units, which roughly corresponds to a municipal sewage treatment plant in a small town. The cleaning process is purely biological. The sewage treatment plant has been carefully integrated into the natural environment of the surrounding landscape and here, too, the most important parameters are checked and monitored by our data collection system.
We are also a member of the DWA association, a politically and economically independent association that works for safe and sustainable water and waste management. It drafts technical standards, contributes to standardisation efforts, supports research and promotes training and further education on the subject in companies.
Our energy and environmental management
Our 3 locations have been certified in accordance with the energy management system DIN ISO 50001 (Vechta and Mönchengladbach since 2014, Erding since 2016) and meet the ever-changing challenges in annual audits. A team of approx. 10 employees is committed to achieving our strategically formulated energy goals and is constantly working on new projects to increase energy efficiency in the company.
Our employees learn about responsible use of energy, resources and the environment in annual training courses conducted by an energy management officer. In addition, a comprehensive monitoring system records relevant key figures from all three locations in order to facilitate benchmarking.